Floating Roof Tank Seals
With over 40 years combined experience of floating roof seals and drain systems for floating roof storage tanks our engineering team can adapt any of our seal designs to suit your particular roof configuration. In particular if you have tanks that suffer from tank shell distortion we can tailor make a sealing system that will provide an effective sealing solution.
We can also quote & supply for replacement parts (retro-fit) for older types of Seals subject to suitable drawings being supplied by the purchaser.
All our Floating roof tank seals are designed to withstand environmental conditions, stored product, tank data including rim space data/out of roundness surveys, & emission control.
Different types of seals & combinations are available to suit pontoon & double deck external floating roof tanks & fixed roof tanks with pan deck roofs or aluminium decks.
Floating roof tank seals normally fall into 3 different categories :-
- Primary Seals
- Secondary Seals
- Double Seals
Please read our guide on Floating Roof Seals as below. Links to our catalogue pages are on the left.
Primary Seals
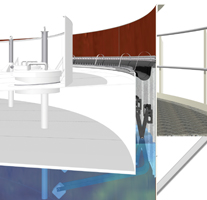
Mechanical Seals : Suitable for tanks without appreciable tank shell distortion or where the product stored is particularly aggressive. Unsuitable for distorted tanks shells or where shell coatings have been applied.
The counterweight system (PT-1) is preferred to the coil spring or pusher bar system as the sealing pressure is constant over time.
Sealing rings (Shoe Plates) are normally supplied in 1.6mm Galvanised Steel but stainless steel can be provided where corrosion is known to be a problem.
The standard material for the continuous fabric seal is a special blend of PVC Nitrile on nylon fabric. For service with aggressive products such as Benzene, Toluene etc, PTFE or Viton can be supplied. Where fire resistance is important, "Firescreen" should be used.
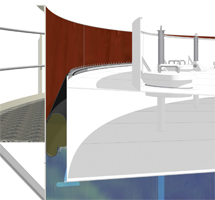
Liquid Seals : Suitable for all tanks but particularly where tank shell distortion is present. The Tubeseal design is preferred to the PT-5 (SR5) design as the sealing liquid is contained in a separate inner tube.
Both seals are product mounted and therefore in the highest efficiency category as defined in API Publication Chapter 19.
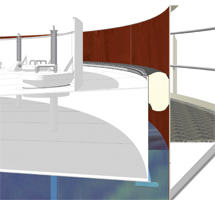
Foam Seals : Used either as vapour mounted (not in contact with the stored product) or liquid/product mounted. Product mounting is much more efficient. Care must be taken to ensure that the tank shell surface is free from sharp edges to avoid damage to the polymeric casing. The seal envelope may be either PVC Nitrile (suitable for service in direct contact with up to 70% aromatics and in vapour contact with up to 100% aromatics), Polyurethane (suitable for up to 100% aromatic service in either direct or vapour contact, but not for certain aggressive chemicals such as Benzene, Toluene or Xylene), or Viton (suitable for virtually all services except MTBE).
Secondary Seals
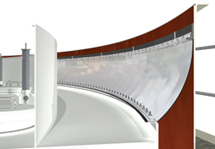
Rim Mounted Seals : Rim mounted secondary seals are fixed at the top of the rim plate on the floating roof. These seals are always fitted above a conventional primary seal. A tight fitting secondary seal acts as an excellent secondary vapour barrier containment & also protects the tank contents & primary seal against weather elements & debris.
The most efficient secondary seal design is the PT-S1 because :-
- The Wiper has a large contact depth with the tank shell.
- It incorporates a continuous vapour barrier membrane for optimum sealing efficiency.
- The compression plates overlap but are not bolted together thus giving a very flexible seal, better able to compensate for tank shell deformations.
- It is supplied with all necessary holes pre-punched to give minimum installation time.
- The seal will re-enter the tank without damage or tendency to hang up in the accidental event of overfilling of the tank.
The PT-S2 type design is a lower cost solution with no vapour barrier membrane and in which the compression plates are bolted together with a gasket in between to form the seal. Drilling of holes on site is required in order to assemble the wiper seal. The PT-S2 can be supplied with a vapour barrier membrane to replace bolting the plates thus giving a more flexible seal.
The PT-S3 type design is similar to that of the Gasket-tite, but with a double-tip type wiper.
Shoe Mounted Secondary Seals : Are used only on primary shoe mounted seals. These seals are fixed at the top of the shoe plate & offer a basic low cost secondary vapour barrier containment. As per API 650, these seals are now normally restricted to use on internal floating roof tanks.
Secondary Wiper Seals : Are commonly used on internal floating roof tanks with a suitable primary seal installed below. These consist of either a wedge shaped Rubber or Foam extrusion bolted to the pontoon rim.
Double Seals
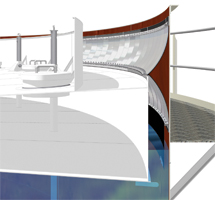
The most effective double seal is the Tubeseal primary seal with the PT-S1 secondary seal. Of the compression plate designs of double seal the most effective seal is the PT-D1 for the reasons given in the section on the PT-S1 Secondary Seal.
Material selection for secondary and double seals should be made using the same guidance given for primary seals.
Seal Failures
Most Seal failures occur as a result of one or more of the following factors :-
- Incorrect rim space data. Most seal specifications will say "nominal rim space 200mm" when the actual rim space is much greater and involves ovality.
- Incorrect material selection for the intended service.
- Incorrect seal selection for the tank configuration (ovality, condition of tank shell weld seams etc).
- Incorrect installation techniques.
Finally, it is vital that the seal components are manufactured from materials that have been proven in service under all climatic conditions.
Should you wish to discuss a particular sealing problem, please do not hesitate to contact us.